Automobilul electric: Totul despre secretele BMW i3
alte articole
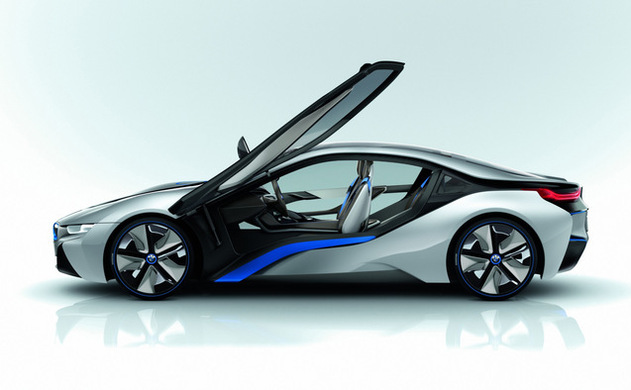
Modul în care privim automobilul va fi schimbat complet odată cu apariţia noii game de automobile electrice BMW i, şi aceasta nu doar din perspectiva propulsiei electrice.
În premieră, va fi utilizată la scara largă fibra de carbon pentru realizarea caroseriei unui automobil de serie mare.
În cazul acestei serii de automobile, preocuparea pentru emisii zero începe încă de la procesul de producţie - pentru care BMW Group va folosi exclusiv energie din surse regenerabile.
În plus, o serie de servicii extinse oferă o experienţă unică a condusului electric, asigurând, de exemplu, utilizarea optimă a infrastructurii de condus.
1. Fibra de carbon în prim-plan
Un factor foarte important pentru automobilele cu propulsie electrică îl reprezintă utilizarea constantă a materialelor ultrauşoare, întrucât, pe lângă capacitatea limitată a acumulatorului, masa maşinii este un factor de limitare a autonomiei.
Cu alte cuvinte, cu cât este mai uşor un automobil, cu atât este mai mare autonomia, pentru că este mai mică masa pe care electromotorul trebuie să o pună în mişcare la accelerare. În plus, în special în trafic urban, fazele de frânare şi accelerare alternează frecvent.
Pe de altă parte, masa redusă a maşinii înseamnă un consum mai mic de putere şi o dinamică mai bună, iar acumulatorul poate fi mai mic.
Utilizarea CFRP la scara industrială
BMW i utilizează constant construcţii ultrauşoare şi materiale inovatoare în automobilele sale - pentru a compensa plusul de masă al componentelor electrice, iar unul din importantele avantaje oferite de soluţia BMW este un concept dezvoltat de la zero pentru propulsia electrică, nu un automobil adaptat de la un model convenţional.
Aşa a apărut o structură completă nouă, aşa-numitul concept LifeDrive, cu o caroserie din fibră de cabon (Life) şi un şasiu construit din aluminiu (Drive).
Celula pasagerilor de la viitorul BMW i3, modulul Life, este realizată în principal din plastic ranforsat cu fibră de carbon (CFRP), iar utilizarea pe scară largă a acestui material de avangardă, uşor şi rezistent la impact, este fără precedent în producţia de serie a unui automobil.
Acest material deosebit era rezervat până acum doar modelelor sport construite în număr limitat, utilizarea extinsă a CFRP fiind considerată ca prea scumpă, iar procesarea şi prelucrarea - prea complexe şi insuficient de flexibile.
Din fericire, BMW a descoperit potenţialul de care dispune materialul şi, după 10 ani de cercetare intensivă şi optimizare a procesului, a materialelor, a sistemelor şi a uneltelor, BMW Group este singurul constructor auto care deţine experienţa necesară pentru producţia CFRP la scara industrială.
Nivelul avansat al procesului de producţie este vizibil mai ales în siguranţa procesului, timpii scurţi ai ciclului şi standardul ridicat de calitate al componentelor produse din CFRP.
Este adevărat că materialele pentru construcţii ultrauşoare precum aluminiul sau fibra de carbon necesită un consum mai mare de energie pentru a fi prelucrate decât oţelul, de aceea BMW acordă, în cadrul prelucrării şi procesării, o importanţă maximă economisirii resurselor şi utilizării vaste a energiei care nu produce CO2.
Principala preocupare o reprezintă consumul de energie şi de apă, procesarea apei reziduale, emisiile de solvenţii şi deşeurile, iar economiile sunt un rezultat direct al noului concept de producţie. BMW Group deţine în asociere cu SGL Automotive Carbon Fibers (ACF) o poziţie unică în industrie ca "proprietar" în toate etapele procesului, de la producţie până la reciclare.
Fabrica de CFRP de la Moses Lake, SUA
Pentru producerea fibrei de carbon la SGL ACF, la fabrica Moses Lake (SUA) se utilizează un material precursor - fibra textilă de termoplastic, realizată din poliacrilonitril.
La Moses Lake, toată energia pentru producerea fibrei de carbon se obţine din surse regenerabile de la hidrocentralele locale, astfel că emisiile CO2 sunt nule şi, în plus, uzina ultramodernă din statul Washington impune standardul şi în privinţa eficienţei energetice.
Reducerea CO2e (potenţial de încălzire globală) este de aproximativ 50% în comparaţie cu producţia convenţională de CFRP.
BMW i3 este programat să părăsească linia de asamblare de la Leipzig la finalul anului 2013, iar pentru aceasta fibrele ultrauşoare au fost produse încă de la sfârşitul anului 2011.
Furnizarea necesarului de materie primă este asigurată de două linii de producţie, fiecare cu o capacitate anuală de 1.500 de tone, ceea ce constituie aproximativ 10% din producţia globală de CFRP din prezent.
Cele două companii-mamă - BMW Group şi SGL Group - au investit până în prezent aproximativ 100 de milioane de dolari în facilitatea de producţie din Moses Lake şi au creat 80 de noi locuri de muncă.
La Wackersdorf, Landshut şi Leipzig, alte procesări
La uzina Wackersdorf Innovation Park, în Germania, legăturile de fibre produse la Moses Lake sunt procesate suplimentar, la scara industrială, într-o structură textilă.
La această unitate industrială, spre deosebire de ţesături, care sunt împletite sau întreţesute, fibrele sunt aranjate unele lângă altele pe un singur nivel, întrucât o structură ţesută ar îndoi fibrele şi ar reduce proprietăţile excelente, pentru că însăşi alinierea fibrei în ţesătură este cea care garantează caracteristicile optime ale componentei produsă în procesul final.
După o investiţie de 20 de milioane de euro şi crearea de aproximativ 100 de locuri de muncă, mai multe tone de ţesătură din fibră de carbon pot fi produse anual la uzina Wackersdorf, care reprezintă materialul de bază pentru producţia pieselor şi componentelor din CFRP la uzinele BMW din Landshut şi Leipzig.
În etapa următoare, ţesăturile din fibră de carbon livrate de la Wackersdorf sunt procesate suplimentar în piese CFRP pentru caroserie la uzinele de presare din Landshut şi Leipzig, unde se produc deja acoperişul modelelor BMW M3 şi M6 şi suportul barelor de la BMW M6.
Recent inaugurată, uzina de presare din Leipzig este echipată cu tehnologie de ultimă oră pentru CFRP în producţia de automobile, ceea ce face ca BMW să fabrice propriile materiale compozite cu fibră de carbon.
Compoziţia, rezistenţa şi geometria pieselor CFRP, pe scurt formula acesteia, poate fi modificată sau adaptată individual în uzina de presare, în orice moment al procesului de fabricare în funcţie de specificaţiile de design.
Reciclarea CFRP şi BMW i
BMW Group a creat de-a lungul dezvoltării BMW i în premieră mondială primul concept de reciclare pentru producţia de serie a componentelor CFRP, a componentelor caroseriei şi a deşeurilor de producţie.
Resturi de materiale obţinute în faza de producţie, dar şi de la automobile distruse sau casate sunt refolosite prin diferite proceduri în construcţia de maşini şi reintroduse în procesul de producţie sau utilizate în alte aplicaţii.
2. Impact minim asupra mediului
Producerea modelului cu propulsie electrică BMW i3 începe în toamna anului 2013 la uzina din Leipzig, unde utilizează surse de energie care nu emit CO2, apoi, la începutul anului 2014, va urma BMW i8, o maşină sport hibrid plug-in cu electromotor, dar şi motor cu ardere internă.
Referitor la protecţia mediului, producerea modelelor BMW i impune noi standarde, printr-un consum de energie mai mic cu aproximativ 50% şi unul de apă redus cu 70% comparativ cu media producţiei BMW, una deja foarte eficientă.
Întreaga cantitate de electricitate utilizată la producţia modelelor BMW i în uzina din Leipzig este generată de centrale eoliene, adică surse de energie 100% regenerabilă.
Sistemele eoliene au fost instalate - în premieră pentru Germania - chiar pe terenul uzinei unui constructor auto, pentru alimentarea directă a locaţiei de producţie, iar activitatea de construire a celor patru turbine eoliene, fiecare cu o putere de 2,5 MW, va fi încheiată în primăvară.
Mai mult, turbinele eoliene produc mai multă energie decât este necesară pentru producţie la Leipzig şi se anticipează un surplus anual de până la 2 GWh, care poate fi utilizat în alte secţii ale uzinei.
Reprezentanţii BMW Group mai precizează că impactul asupra mediului al întregului automobil este definit mai ales de faza de utilizare, unde construcţia ultrauşoară - în special - îşi demonstrează potenţialul de economisire.
Construcţia uşoară în sine face ca BMW i3 să fie mai eficient din perspectiva energiei pentru întregul ciclu producţie-utilizare-reciclare, deşi costurile de producţie (acumulator, construire CFRP ultrauşoară) sunt mai mari din punct de vedere energetic în comparaţie cu materialele convenţionale.
BMW Group a controlat încă de la început emisiile CO2 generate prin consumul de energie pentru procesul de producţie, iar BMW i3 demonstrează clar succesul acestor eforturi.
De-a lungul întregului ciclu de producţie şi de viaţă, incluzând şi generarea energiei în Europa utilizată la încărcare (mix de energie electrică EU-25), automobilul electric dovedeşte un impact asupra mediului (CO2e) mai mic cu cel puţin o treime decât o maşină similară ca eficienţă, dar cu motor cu ardere internă.
Mai exact, dacă energia pentru condusul automobilului este obţinută din surse regenerabile precum energie eoliană sau hidro, potenţialul de încălzire globală poate fi redus cu peste 50%.
3. Acumulatorul BMW i3 are o autonomie de 160 de km
Referitor la sursa de energie furnizată pentru BMW i3, aceasta provine de la un acumulator litiu-ion foarte performant, special dezvoltat pentru model, care include 96 de celule grupate în 8 module.
Asigurând o distribuţie excelentă de mase între punţi şi un centru de greutate foarte jos, bateria este integrată compact sub podea, unde este protejată în mod optim.
Pentru găsirea echilibrului optim între performanţe, autonomie, masă şi durată de viaţă, acumulatorul a fost optimizat continuu de-a lungul perioadei de dezvoltare, iar celulele de stocare au aceeaşi durată de viaţa ca şi automobilul.
BMW i3 are o autonomie de 160 de km în condiţii normale când este complet încărcat.
Aşa cum au demonstrat testele cu MINI E, BMW i3 este utilizat în special în oraşe şi ca maşină de navetă între birou şi domiciliu, dar este potrivit şi pentru zone de periferie.
Peste 1.000 de potenţiali clienţi au parcurs de-a lungul probelor cu MINI E şi BMW ActiveE peste 20 de milioane de kilometri în 10 ţări, iar testele au arătat că aproximativ 90% din călătoriile zilnice acoperă în medie 45 de km, astfel că BMW i3 îndeplineşte necesităţile utilizării cotidiene în zonele urbane.
Pe de altă parte, încărcarea BMW i3 este foarte simplă şi la punctul de încărcare de acasă, indiferent că este o priză clasică sau un panou BMW i, acumulatorul BMW i3 este complet încărcat după minimum şase ore.
Astfel, cu ajutorul unui dispozitiv public modern de reîncărcare rapidă, bateria este adusă la 80% din capacitate în 30 de minute, pentru alţi 120 de kilometri.
Totodată, pentru a uşura utilizarea optimă a BMW i3, BMW i furnizează o gamă completă de produse şi servicii care acoperă nevoile personale ale clienţilor dincolo de automobil, iar clienţii aleg produsele şi serviciile pe care le vor.
Pentru aceasta, portofoliul 360° ELECTRIC se bazează pe patru principii de bază: Încărcarea acasă, Încărcarea la staţii publice, Asigurarea mobilităţii şi Integrarea în concepte inovatoare de mobilitate pentru depăşirea limitărilor de autonomie.
Posibilitatea de reparare a structurii CFRP de la modulul Life a fost în fruntea listei cu specificaţiile tehnice - de exemplu, numeroase secţiuni de reparaţii au fost definite pentru rama laterală.
Spre exemplu - dacă un prag lateral afectat trebuie înlocuit după un impact lateral, atelierul realizează o inspecţie vizuală şi o constatare a pagubelor, după care scoate doar secţiunea afectată a pragului lateral prin utilizarea unui instrument patentat de frezat.
Un alt avantaj este că orice dealer autorizat BMW i poate efectua reparaţii exterioare. Datorită particularităţilor modulului LifeDrive - specifice produsului -, vor exista centre de reparaţii în care angajaţi specializaţi vor repara maşinile cu daune la structura de aluminiu sau CFRP.